WHAT IS A SLIP RING?
Measured on size alone, a slip ring is a relatively small piece of a larger engineering puzzle, but looks – as they say – can be deceiving. Slip rings are actually a vital electromechanical device that you’ll find as a commonplace component in many of today’s industrial, military and even everyday equipment, where they play a crucial role in answering one of engineering’s most difficult questions:
How do you efficiently – and effectively – transfer power and other electrical signals from a stationary device, component or power source to a rotating object?
Slip rings ensure engineering and design teams no longer require timely – and often costly – workarounds in order to power rotating devices, whether they be motors, military devices or rotating electrical assemblies. Playing a major role in improving mechanical performance, as well as simplifying operations, they have further further eliminated the threat of damaged and hazardous wiring and cable connections in moving joints.
Slip rings handle either power, data or both across a number of rings on which a spring or other loaded contact finger, ring or brush is held in place to pass power as the rings rotate.
Power levels range from milliwatts to hundreds of kilowatts dependent on application.
In all applications, frictional wear is the main determinant of the lifecycle of the slip ring.
Many of these systems have migrated to using precious metals like gold and silver to increase lifecycle. Dependent on speed, power level and environmental condition, the number of expected rotations before replacement is needed ranges from a few million to 10s of millions.
With the advent of contactless, wireless power technologies, slip rings are once again taking their next evolutionary step to fulfill the growing needs of modern designs, just as current slip ring varieties have done so in the past. With these wireless slip rings, power and signals are able to be delivered to rotating devices more efficiently – and cost effectively – than ever before.
HOW DOES A SLIP RING WORK?
So we know that Slip Rings are able to transfer power or signals across a rotating surface. But how, exactly, do they do this? At a very elementary level, a slip ring is comprised of two major components – a metal brush, and a metal ring. The brush (or brushes) are in contact with the metal ring as it rotates. The resulting friction then causes an electrical signal which delivers the power.
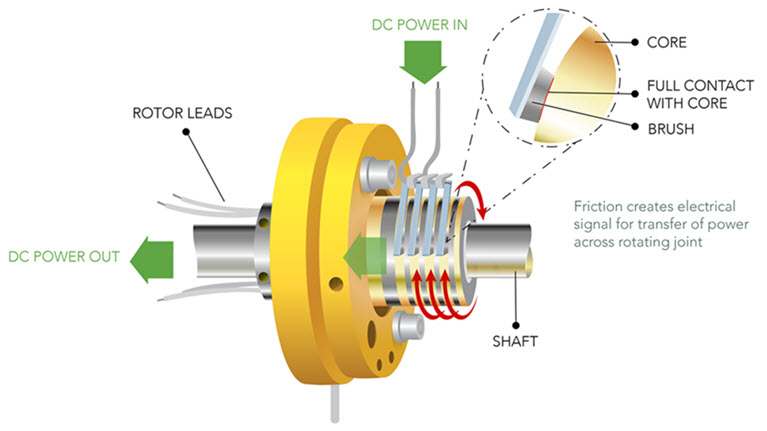
The ring itself is a band of electrically conductive material, mounted on a shaft. Although it’s insulated from the shaft itself, the slip ring is connected to the rotor or rotating assembly through wingdings or other electrical connections.
The outer part of this slip ring remains in continuous sliding contact with the stationary brushes – or other stationary conductors – which provides either intermittent or continuous rotating devices with unbroken contact between the rotating assembly and external circuit. This ensures power and data are able to be transmitted at all times.
Both this ring and the brush are contained within a single housing, designed to protect the working parts from harmful environmental factors such as dust and moisture.
THE COMPONENTS OF A STANDARD MECHANICAL SLIP RING
Slip rings may appear to be complicated devices, yet most all standard mechanical slip rings can be easily broken down into two major components, as already mentioned:
The Brush
The brush is a stationary contact made of either graphite or metal, which then rubs against the outside of the rotating metal ring. Made from metal fibers, this brush can look like any regular brush, though more often than not it’s usually a single wire or a spring with a pad of material attached to the end that makes physical contact with the ring.
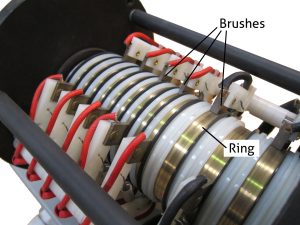
The Ring
The ring is constantly rotating, and as it does so it conducts electrical currents or signals via the stationary brush.
The number of rings found in any given slip ring can vary depending on the needs of the device, with additional assemblies – a combination of both brush and ring – stacked along the main rotating axis – or shaft – if more electrical circuits are required.
The insulation between the shaft and ring is generally made of any number of synthetic materials, including nylon and phenolic plastic.
For the effective use of a slip ring, the ring itself needs to be properly matched with the right brush, which is why they’re often sold as a set, known as a slip ring Assembly. These sets usually serve most component replacement requirements, or alternatively can be used as parts for custom assembly designers with a little mechanical engineering know-how.
Slip rings can be designed in a variety of configurations. For example they can provide an open through-bore to accommodate other components such as a fluid joint or a wave guide. Instead of a drum the rings can be configured in a platter or pancake. This is appropriate if the space available for the slip ring is short and wide instead of tall and narrow.
A critical aspect of slip ring design is the materials used to make the rings and the brushes. After World War II manufacturers responded to requirements from the emerging electronics industry with gold plated rings using gold wire brushes. Up until the 1970’s many slip rings used copper rings and graphite brushes. Copper is smooth and conducts electricity well. Graphite conducts well, it is soft, and it does not abrade the copper rings. But for advanced applications such as space satellites and missiles, graphite brushes were inadequate. There was a burst of research and invention in the early years of the space program to address emerging needs, mostly in space and missile programs, that produced advanced gold on gold alloy systems and systems that employed silver alloy rings with brush tips made from silver graphite mixtures. Today these two systems, gold-on-gold and silver/silver-graphite, are the mainstays of the slip ring industry. Gold-on-gold systems are often used for low current signal circuits because they are compact. Silver/Silver-graphite systems are often selected for higher current power circuits because in these applications they are more economical, and have long service life.
WHERE ARE SLIP RINGS MOST COMMONLY FOUND?
Slip rings are utilised in a variety of devices across a broad range of industries. Some of these include:
TRUCKS & MANLIFT EQUIPMENT:
Aerial Work Platforms
Bridge Cranes
Platform Cranes
INDUSTRIAL/COMMERCIAL IN-PLANT EQUIPMENT:
Automated Welding Equipment
Centrifuges
Conveyor Systems
Custom Machinery
Fabrication Equipment
DRILLING & OTHER BORING EQUIPMENT:
Off-Shore Drilling Rigs
Down hole Drill and Geotechnical Testing
Horizontal Earth Boring & Drilling
SIGNAGE RELATED EQUIPMENT:
Advertising Displays
Exhibits and Displays
MISC. OFF-HIGHWAY HEAVY EQUIPMENT:
Forklifts
Utility Trucks
Truck Body / Service Cranes
OTHER:
Amusement Rides
Arcade Machines
Car Wash Equipment
Wind Turbines TYPES OF SLIP RINGS
CONTACTLESS, WIRELESS SLIP RINGS
Contactless, wireless slip rings are the next generation in inductive power transfer solutions, specifically designed to replace existing, aging mechanical slip ring technology. Moving on from a reliance on friction based metal and carbon brush contact to enable the transfer of power and data, wireless slip rings utilise IPT to transfer power via an electromagnetic field created by coils placed in the stationary transmitter and rotating receiver.
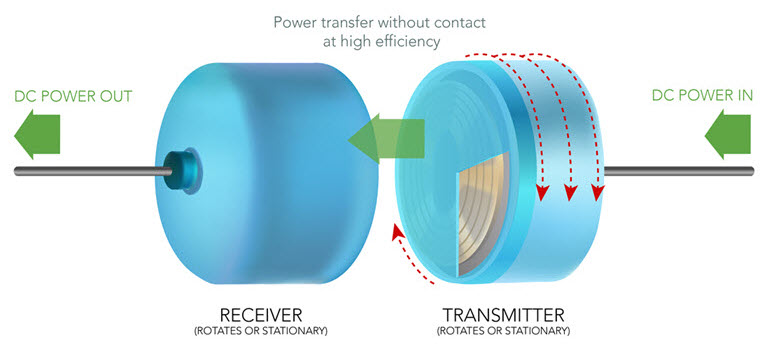
By removing the inherent need for friction or contact to generate an electrical current, wireless slip rings significantly reduce the maintenance costs associated with worn mechanical slip rings, while also offering a simple, clean design that’s easily integrated into any application or device.
MINIATURE & CAPSULE SLIP RINGS
As the name suggests, miniature and capsule slip rings are the smaller, more compact counterpart of their regular sized cousin, yet despite this downsizing they still feature many of the same features and capabilities.
Often used in small and medium sized equipment – particularly the security industry where they’re often found in CCTV equipment and other small rotating systems, such as revolving stage lights – miniature and capsule slip rings generally measure 22mm in diameter, and facilitate the transfer of video, control, sensor, power and ethernet.
MERCURY WETTED SLIP RINGS
While they may share the name, Mercury Wetted slip rings differ in a number of crucial ways. Their major point of difference is that they replace the regular metal or graphite sliding brush contact of a standard, mechanical slip ring with a pool of liquid metal, which is molecularly bonded to the contact.
This change affects the fundamental operation of this variety of slip ring: as they rotate, the liquid metal maintains the electrical connection between both the stationary and rotating contacts, much like a brush would in a regular slip ring.
Mercury Wetted slip rings do suffer from one major flaw: safety. The use of mercury presents numerous safety concerns, as mercury is, after all, a toxic substance. This inherent safety risk has seen mercury wetted slip rings prohibited from use in a number of environments and industries, including:
Food manufacturing and processing
Pharmaceutical equipment
Other uses where contamination could present a serious health and safety threat.
PANCAKE SLIP RINGS
As the name implies, the conductors of a Pancake slip ring are arranged on a flat disc – much like a pancake – as concentric rings centered on the rotating shaft. Insulating material is then used between these concentric rings, while the brushes are distributed on the top.
The form factor provides Pancake Slip Rings with major advantages, making them a perfect fit for electrical conduction in narrow, smaller spaces where regular slip rings just wouldn’t work.
However the unique configuration does have its drawbacks. Namely, pancake slip rings are often much heavier in both weight and volume for the same capacity circuit of a regular slip ring, while also exhibiting greater capacitance and crosstalk, as well as increased brush wear which more readily collects on its vertical axis. This propensity for wear and tear means pancake slip rings often suffer from an increased need for maintenance and repairs over their lifetime, resulting in a higher maintenance cost.
LEADING CAUSES OF SLIP RING FAILURE
It’s common knowledge that standard mechanical slip rings are prone to failure, particularly in dirty, dusty or outdoor environments where machinery and equipment is exposed to debris, water and other environmental factors. The most common cause of failure is often attributed to sticking brushes, however there are numerous issues that can lead to the need for maintenance and – at times – outright replacement of mechanical slip rings.
THREADING OF BRUSHES
The initial signs of brush threading can often be found on the commutator or ring itself, where fine grooves begin to form. These are usually created by high levels of friction causing small particles of copper to wear away from the commutator, which then becomes embedded in the brush face resulting in scratches on the commutator.
Atmospheric contamination including dirt and dust is also known to cause threading, with particles gathering on the slip ring and brushes gradually wearing away at the commutator during operation.
GROOVING
As with any device or component, uniform wear around the circumference of the rings – known as ‘Grooving’ – is commonplace. However higher levels of wear requiring regular maintenance demands further investigation as this can often point to more serious, ongoing issues.
POLARITY WEAR
In scenarios where slip ring polarities are separate, including the likes of synchronous motors or generators, one ring may suffer from more wear than the other. This is often referred to as ‘Polarity Wear’.
SELECTIVITY
Uneven currents in parallel paths affects the wear rates of slip ring brushes, with no two brushes ever wearing at the same rate. Though as with any mechanical component, brushes operating at higher temperatures and currents generally wear faster than those operating under less extreme conditions.
LOSS OF BRUSH CONTACT
The loss of contact between brush and ring can result in a shortened brush lifespan, and cause damage to the ring surface. This is often a result of weak brush springs, but can also be attributed to abnormal vibrations, brushes becoming hung up in holders, as well as brushes wearing too short over time.
RING CORROSION
Steel slip rings that operate in damp or wet environments are susceptible to rust, while copper bearing materials are also prone to reacting to acids as well as various sulfur compounds found in the air.
It’s these scenarios where hermetically sealed & waterproof wireless slip rings have a distinct advantage as there no direct contact and no friction causing the breakdown in power delivery.
HOW DOES A WIRELESS SLIP RING WORK?
Wireless slip rings are based on fundamental Inductive Power Transfer technology whereby specially tuned copper coils transfer AC power via an electromagnetic field.
The diagram below highlights the basic technology:
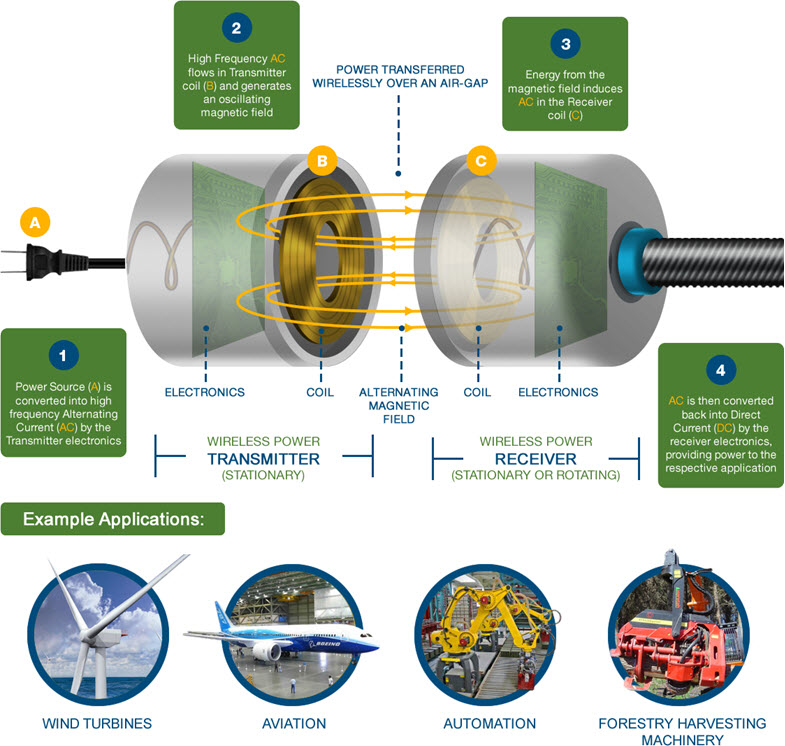
THE ADVANTAGES OF WIRELESS SLIP RINGS
Contactless, brushless and
providing complete freedom of movement, Slip Rings offer countless advantages over their aging, mechanical counterparts.
1) Provides highly efficient transfer of power and data across short distances through inductive power transfer
2) Eliminates friction or heating between rotating and stationary circuit contacts, with a fully brushless, contactless design
3) Complete freedom of movement, high RPM and no need for lubrication and cooling
4) Cost-effective, maintenance-free alternative to traditional mechanical slip rings
5) Solves the issue of continuity of power & data delivery
6) Specially manufactured for an easy hassle free, seamless, plug-and-play replacement for existing mechanical slip ring components
THE HISTORY OF SLIP RING DESIGN
Today, slip rings are commonly manufactured from any number of conductive materials, though you’ll typically find that this is a combination of copper or gold alloy contacts, though silver and coin silver are also used in some cases. However, this wasn’t always the case.
Until the late 1970’s, slip rings commonly used copper rings, in combination with graphite brushes. The thinking here was sound: copper is smooth and conductive, while graphite is soft, conducts well and does not abrade or deteriorate the copper rings that they come into contact with in order to transfer the electrical signal or data.
These old copper and graphite brushes soon found their limitations, as fast-advancing industries – including complex aerospace and military applications – required more of their slip rings for mission critical systems. These older designs were unable to cope with the wear, tear and design requirements, which resulted in a flurry of research and innovation that delivered a more robust and viable alternative solution that addressed the emerging needs at the time.
Through this process, an advanced gold-on-gold alloy system was produced, which employed a silver alloy ring in combination with brush tips made of a silver and graphite mixture.
Today, you’ll find both of these systems in active use in various slip ring products, depending on the device and its intended use. Gold-on-gold is often found in lower current signal circuits, thanks to its compact size. While silver and silver graphite slip rings are used in higher-current power circuits, as they are at one more economical and boast a longer service life.
A SLIP RING BY ANY OTHER NAME
While most commonly referred to as slip rings, these devices are also known by a variety of other names, including:
Rotary Electrical Interface
Electrical Rotary Joint
Rotating Electrical Connectors
Collectors or Collector Rings
Swivels or Electrical Swivels
WHAT ARE SLIP RINGS COMMONLY USED TO TRANSFER?
Slip rings aren’t used for just electrical purposes. They can also transfer analog and digital signals – such as data – meaning they’re now commonly found in applications such as aerodrome beacons, rotating tanks, radio telescopes and power shovels.
Video
Communications & Data
Serial Links
ESD Signals
Fibre Optic
HOW SLIP RINGS ARE RATED
Slip rings are available in a number of standard and custom configurations, specifically designed for a given device or the environment they’re operating in. These slip rings are often identified – and classified – by the following attributes:
Speed
Current
Voltage
Insulation
Resistance
Other Factors
Note: The speed of a slip ring is measured by the number of Rotations Per Minute, or RPM. This RPM is then used in combination with the length of use to provide the estimated life span of the slip ring. Where the length of use is multiplied by the speed at which it will operate.
SLIP RING REPAIR & MAINTENANCE – WHY IT’S IMPORTANT
Regular maintenance of slip ring hardware is paramount for both personal and operator safety, as well as ensuring maximum service life of the slip ring in question. This maintenance and servicing regime is usually provided by the slip ring manufacturer or a qualified engineer, who supply ongoing maintenance, servicing, tests and repairs.
This maintenance usually runs on a schedule, with a yearly inspection followed by proper maintenance once every 5-8 years. While it can be costly, regular maintenance can save the operator from prolonged downtime and repairs in the long run as major malfunctions or failures are avoided.
The maintenance required often varies depending on the current number of rotations performed by the slip ring, as well as the environment it has been operating within. The more demanding the environment, the more wear and tear it will exhibit. Though some, and in fact most, slip rings very rarely require maintenance at all, as they never reach the required number of revolutions to need maintenance.
WHAT IS THE DIFFERENCE BETWEEN A SLIP RING AND BRUSH?
Rather than a separate device, a brush is actually a major component of a slip ring. These brushes are blocks of either graphite or carbon material, with conductive mountings that are then connected to the system outside of the rotating components. When operational, the ring makes contact with these brushes as it rotates, effectively – and continuously – providing a transfer of electrical power or data signals.
WHAT IS THE DIFFERENCE BETWEEN A SLIP RING AND COMMUTATOR?
Slip Rings and Commutators are often mistakenly referred to as the same device, however they both fulfill very different needs. A commutator is a specialised slip ring, which you’ll find primarily used in likes of direct current (DC) motors and electrical generators. It’s here that they transfer electrical power between stationary housing and the rotating armature with the added purpose of reversing the electrical current direction.
Unlike the solid metal ring of a standard slip ring, commutators are made of insulated metal segments, with electrical brushes (contacts) then rubbing on the ring as it rotates to make the electrical connection.
The ring segments of a commutator have also been specially wired to act as a rotary switch in order to reverse the electrical current. In a DC motor, this switching reverses the magnetic field and keeps the motor turning. In a generator, for example, this switching changes alternating current (AC) into current flowing in one direction (DC).
WHAT IS THE DIFFERENCE BETWEEN A SLIP RING COMMUTATOR & SPLIT RING COMMUTATOR?
While they may sound the same, a Slip Ring Commutator and Split Ring Commutator fulfill two very different roles. A Slip Ring commutator maintains a connection between the moving rotor and the stationary stator, providing AC current. While a Split Ring Commutator functions differently, by changing the direction every half rotation, and is used to get a pulsating voltage – for example, in the case of a direct current (DC) motor. |